Hydrokinetic
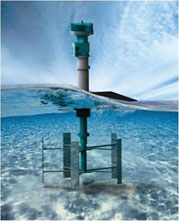
Source: New Energy Corporation www.newenergycorp.ca
Recent innovations are driving new interest in an old technology – hydrokinetic power. Systems use the kinetic energy, or velocity head, of a flow by placing the turbine in a river or canal. Hydrokinetic power differs from conventional hydropower, which uses the potential energy or pressure head of the water to generate energy. Hydrokinetic systems require relatively high flow velocities and sufficient water depth to maintain submergence of the turbine. The potential to extract energy from the flow is related to the swept area of the turbine and the velocity cubed, much like a wind turbine. Hydrokinetic systems can only extract a fraction of the power from the water compared to conventional hydropower systems; hydrokinetic turbines are based on the kinetic energy of the flow only and not the potential energy from pressure head. The majority of hydrokinetic turbines are still in the prototype phase, with a small number of companies offering commercial products. Commercial hydrokinetic turbines range in size from 5 kW to 250 kW and cost around $4,000 per installed kW. Compared to other forms of hydropower generation, hydrokinetic turbines are relatively expensive. Typically, conventional hydropower systems cost around $2,000 per installed kW. Hydrokinetic systems often appear simple to deploy, but low production relative to installed cost leads to a less cost-effective system than many conventional hydropower installations. Environmental issues can still impact the feasibility of hydrokinetic systems and can include impacts to aquatic life, erosion, and flow alteration.
The canal installation shown below is a Hydrovolts turbine installed for six weeks as a test program in the Roza Canal in Oregon. The turbine produces 5 kW with 6.5 ft/sec of water velocity. The canal is cement lined and 14 feet wide at the bottom with a maximum water depth of 11 feet. The canal flows between 1,100 and 2,100 cfs. The installation of this turbine requires little civil infrastructure, although the canal must have adequate geometry and freeboard to handle the resulting rise in water surface elevation upstream of the turbine (6-8 inches).xii
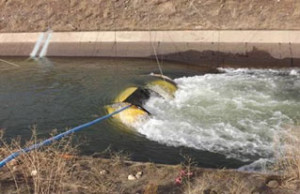
Source: The Colorado Energy Office “The Small Hydropower Handbook”
Hydro-mechanical
Hydro-mechanical systems use hydro turbines to supply mechanical work to machinery instead of electric generators. Historic uses include sawmills, textile mills, and grain mills. In the present day, hydro-mechanical energy can be used to drive sprinkler irrigation systems. Most center pivot sprinklers use hydraulic or electric motors to drive the wheels. In cases where excess head is available, a hydro-mechanical turbine can power a hydraulic pump, which in turn drives the hydraulic motors that propel the sprinkler. These systems are not feasible where water is pumped to the sprinkler. Since the hydro-mechanical turbine does not generate electricity, installations are not regulated by the Federal Energy Regulatory Commission (FERC). These installations can replace diesel/propane generators or eliminate the need to have electrical service provided to the center pivot. Performance of the sprinkler system may also be increased, as center pivot manufacturers claim hydrostatic drive pivots move more smoothly and do not leave dry areas associated with the start-and-stop electric motor driven units.[i]
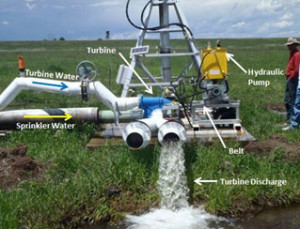
Source: The Colorado Energy Office “The Small Hydropower Handbook”
The Bear River Ranch near Steamboat Springs, Colorado, installed a hydro-mechanical system to power its center pivot irrigation system. The system uses the power of falling water to directly drive and pressurize the center pivot and eliminated the need for electricity and significantly reduced operating expenses. The turbine uses 126 feet of head and 560 gallons per minute to produce the equivalent of 5.2 kW of power, which drives the center pivot. A case study at the end of this handbook describes the system in more detail. xii
[i] Source: T-L Irrigation (www.tlirr.com/difference/continous_movement_hydraulic-drive)